Design Excellence: The Collins PTO
Design Excellence: The Collins PTO
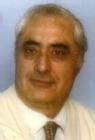
Around the end of WWII, in the golden age of analog designs, Collins set new standards for tuning accuracy and stability in communication equipment, culminated since the early ‘950s in the introduction of digital mechanic readout sets, as the R-390. Specs of these sets were simply exceptional, with overall accuracy and stability figures unsurpassed until the introduction of digital frequency synthesizers. A relevant role was played by the Permeability Tuned Oscillator or PTO used as variable tuning local oscillator. The first known use of a PTO as a replaceable subassembly could be dated around 1945 with the RT-91/ARC-2 transceiver. Some details evolved in the years, as the tuning range and the turns of the tuning shaft, the use of miniaturized components and of subminiature tubes or even semiconductors, or the use of a temperature controlled oven for models to be operated in extreme environmental conditions. Nevertheless the basic design remained unchanged for about a quarter of a century.
Collins permeability tuned oscillators are listed in the table below. Click on the thumbnail of the pages to enlarge them.
Table 1 - List of Collins permeability tuned oscillators.
Here is a little survey of permeability tuned oscillators, most from Collins, a couple from some of the several second sources grown for the military market.
Fig. 1
- 1A, the 70E-15 PTO is used in the 51J line; 2.0 to 3.0MHz over 10 shaft turns.
- 1B, the 70E18 is the variable oscillator of the R-392 vehicular receiver; 2.455 to 3.455MHz over 10 turns, 26VDC heater and B+ supply.
- 1C, this is a thermostatic 70E-22 PTO used in the RT-311/ARC-38 airborne transceiver; 1.75 to 3.5MHz over 10 turns.
- 2A, the 798 from Progressitron is an appreciated replacement for the Collins 70H-2, the thermostatic PTO used in the R-390/R-390A military receivers; 2.455 to 3.455MHz over 10 turns.
- 2B, the 70H-13 was used in ARC-58 airborne radio set; subminiature tubes, 2.0 to 4.0MHz over 10 turns.
- 2C, the 147A-1 is also used in RT-311/ARC-38; tunes from 200 to 300KHz over 12.5 turns of the shaft.
- 2D, the 70J-2 is the BFO tuning coil used in the R-392 and retains the same hermetic execution and ruggedness of other permeability tuned oscillators.
- 2E, this is an Autodyne 1009, alternate part for the Collins 70J-3 used in the BFO of the R-390A; tunes from 452 to 458KHz.
To give an idea of the exceptional performances reached we can give a look at the specs of the PTO used in the R-390, the 70H-2. The tuning range covers exactly 1MHz, from 3455 to 2455KHz, in exactly 10 turns of the shaft. The non-linearity error is lower than 300Hz. The PTO thermal drift does not exceed 500Hz from –40 to +60 deg. C and its direction has been calculated to compensate drifts of the remaining circuits, so to grant an overall stability of the receiver better than 300Hz from –40 to +65 deg. C. From the figures above, in the R-390 the PTO is about as stable and accurate as the crystal oscillators. Slightly worse figures can be found in the case of a PTO without thermostatic oven, such as the 70E-15 used in the 51J line. Here the overall maximum error, also including errors of the two crystal oscillators, is not greater than 2KHz from –20 to +60 deg. C.
The secrets for the said results can be found in the extreme care of the design and of the engineering of the permeability tuned oscillators. The tuning components are hermetically enclosed in an aluminum can, just leaving outside the tube(s) and the related biasing and decoupling parts. Variable inductance tuning is used to prevent the microphony usually associated with variable capacitors. The winding is logarithmic, to ensure a straight-line frequency tuning. The sintered powder core moves smooth in and out of the coil, driven by a double-threaded tuning shaft and an anti-backlash female screw. To compensate for imperfections in the winding geometry, the advancing of the core is controlled by a factory adjusted cam profile and a spring-loaded cam follower, so making linear the frequency variation through the tuning range. The main tuning capacitor is a precision hermetically sealed ceramic unit, as the 1% tolerance types from Sprague-Herlec, selected for very low temperature coefficient. Small temperature controlled ceramic capacitors are added in parallel to the first one, to get the specified thermal drift. A small variable inductance is added in series to the main one to precisely adjust the frequency end-point. In some PTO models capsules containing dehydrating salt are added to adsorb moisture. Small o-rings seal the bushings of tuning shafts, both the main and the end-point adjusting ones. Figures 3 and 4 below show some details of the 70E-22 and of the 147A-1.
Fig. 3 – This is the internal view of the 70E-22 PTO, showing in the background the main tuning components, the logarithmic wound coil, the tuning core and the threaded shaft. In the foreground, the end-point adjusting coil, the cam, the cam follower and the tuning capacitors, the larger one partly covered by one of the square rods.
Fig. 4 – Two internal views of the 147A-1 PTO. 1A shows the main tuning capacitor, a 2200pF plus/minus 1% sealed unit, characterized for an extremely low temperature coefficient, a mere 7 ppm figure annotated on the body. 4B shows details of the variable tuning parts. The cam profile is formed by some 100 tiny adjustable segments; thin spacers among them allow the adjusting of each segment without disturbing the near ones. The toroid coil on the left is used to obtain a narrower tuning range.
Very few details are given about the components and the calibrating procedures of these subassemblies, with some exceptions for the end-point corrector coils. Often even for the adjustment of this coil special tooling was required, including test cables, a graduated or better a multi-turn knob and sometimes a special screwdriver. Figure 5 shows the special home-made tool for adjusting the corrector coil of the 70E-15. Indeed these units were usually factory sealed while being held at high temperature and had to be returned to the manufacturer or to authorized centers for servicing the components inside the hermetic can.
Fig. 5 – The home-made coaxial screwdriver required for adjusting the end-point of the PTO used in the 51J receivers.
To thank the Author because you find the post helpful or well done.
COSMOS PTO
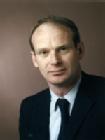
Beside the superior electrical and mechanical design in combination with excellent workmanship Collins gear became famous for their mechanical filters and PTOs. Altogether led to the leadership of Collins for many years.
PTOs as well as e.g. R-390A receivers were not solely produced by Collins but also by several other companies some of which are mentionned in the above article of Emilio Ciardiello. Whereas PTOs built by Motorola were nearly exact copies of the Collins design many 'late' R-390A receivers e.g. from Electronic Assistance Corporation (EAC) preferred PTOs built by COSMOS Industries (NYC). Linearization of the COSMOS PTO was not performed using cumbersome cam followers but a more elaborate mechanical design using a third inductor coil.
PTO on the left side is a newer version (Type 136-1).
To thank the Author because you find the post helpful or well done.
R-390A PTO
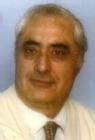
For R-390A and its subassemblies, due to the success of the receiver and to its life, we can find several alternate sources. Some, as Motorola, made exact copies of the original Collins parts, other engineered their own compatible modules.
The sources for R-390A PTOs are:
- Progressitron, considered the best available; Collins design.
- Cosmos, very good, but limited end-point adjustment. Proprietary design with linearizing coil and rotary dish.
- Collins 70H-2, the original.
- Motorola, exact copy of the Collins.
- Dubrow, good replacement with their own cam design.
Full details of the Cosmos PTO can be found here.
Of course all the alternate sources as minimum requirement had to fully comply with the specs of the original Collins PTO to be accepted by military.
But all the above list is just related to R-390A and some of its direct derivatives, while the Collins overall architecture and its advanced engineering solutions influenced the design of any future high-performance communication equipment.
Regards, Emilio
To thank the Author because you find the post helpful or well done.
Jig for measurement and alignment of the 70E-15 PTO
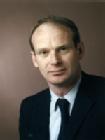
Here I'll present some unpublished data on the 70E-15 PTO.
To properly measure and adjust the 70E-15 PTO as used in Collins 51J-4 (R-388A) receivers the PTO has to be removed from the radio.
I've built a suitable jig that allowed a controlled setting of the rotary angle of the 70E-15 PTO over 10 turns (=3600 degrees) spanning a frequency range from 2.000 to 3.000 kHz. Thus, an increment of exactly 90 degrees changes the output frequency of the PTO by 25 kHz.
PTOs have the tendency to 'shorten', i.e. with time (we are talking about more than 50 years) the actual tuning range becomes smaller than the nominal span of 1.000 kHz. There is provision to compensate for this effect with an end-point adustment coil. End-point errors of up to 15 kHz can be trimmed.
Jig for the measurement and end-point alignment of the 70E-15 PTO
Custom built tool for end-point adjustment
End-point-adjustment of a 70E-15 PTO (SN 1214) that was 11,5 kHz 'off'
Plot of the linearity of two different 70E-15 PTOs (SN 1214: filled circles, SN 2395: open triangles) after end-point adjustment has been performed.
Shown is the percentage of error of the measured frequencies in relation to the nominal frequencies. Next alignment step would be a linearisation proceedure.
To thank the Author because you find the post helpful or well done.