Notes on home-winding mains transformers
Notes on home-winding mains transformers
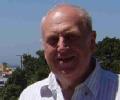
Hi Forum
I was interested in the articles by Joe Sousa and Gerald Bischoff on transformers, and thought I would like to share some experiences with others who would like to make their own small transformers for battery eliminators etc.
1. I usually obtain the small transformer cores I need from clearance sales at electronic stores. I also have a supplier who can provide me with all the other bits - the laminations, plastic bobbins, brown paper and so on.
2. The calculations for the number of turns required and suitable wire gauges may be calculated using the programs for transformers in HAMCALC. HAMCALC can be downloaded from http://www.cq-amateur-radio.com/HamCalcem.html
The calculations seem to be based on the same formulae as those given in "Reference Data for Radio Engineers" They use imperial units.
I have been using a B of 12000 Gauss in the design.
3. For "Rough and Ready" transformers, I often simply unwind the secondary, counting the turns, and then rewind by proportioning the turns. For example, a 51 volt secondary had 1080 turns. If I need an 80 volt secondary, then I need 80 * 1080/51 = 1694 turns. Remember that the output voltage will fall on load in a poorly regulated transformer. Also, here in South Africa we can get a wide variation in supply voltage. The rest of the power supply must be designed to allow for any variations.
The resistor in the illustration below is used to simulate a load on the transformer. The open circuit voltage was a rather high 104 volts, still, good enough for a one valve set.
3. The wire for winding transformers is best used fresh from a new reel, because any small kinks or imperfections can cause local oveheating and premature failure.
4. If you are using a coil winding machine, mandrels to hold the bobbin can be made from threaded rod and supawood. For small transformers, I use a mandrel with two conical holders:
5. For low voltage (e.g filament windings) it often isn't worth the trouble of setting up a coil winder. Most transformers can be wound by hand, albeit with care and patience. I use a Micafil solenoid winder, but many people have had success using a hand drill and turns counter.
6. For transformers with multiple windings, I usually do the high-tension windings followed by a layer of brown paper, then the filament windings followed by a layer of brown paper, finishing off with empire cloth.
7. If you are going to use sellotape to finish off - be sure you design the transformer to run cool!
8. After assembling the core, be sure to squeeze it tight in a vice so that the laminations all fit together tightly.
9. Before bringing the wire out to the terminals, double it back on itself to avoid strain.
10. If connecting flying leads, wrap a few layers of brown paper over the windings, then double the wining wire back on itself and solder the leads, finishing off with more brown paper and finally, empire cloth. This is to avoid putting local pressure on the winding.
Although I have had success with mains transformers, chokes and valve interstage audio transformers, I have to admit I have not been quite so succesful with audio output transformers. (they work, but too much bass) I must leave the design of those to someone who knows how.
Finally, its probably always best to buy ready made transformers, if you can. Alas, for simple valve equipment this isn't always possible.
Good luck
To thank the Author because you find the post helpful or well done.