Röhrenhandel in Deutschland - Erinnerungen eines Insiders
Röhrenhandel in Deutschland - Erinnerungen eines Insiders

Vorwort
Heinz Ebert, Jahrgang 1937, langjähriger Vertriebsleiter für Röhren bei AEG-Telefunken in Ulm an der Donau und später mit seiner eigenen Firma Tubelectron in Röhrengeschäft tätig, hat sich freundlicherweise bereit erklärt, über seine Tätigkeit, Kenntnisse und Erfahrungen im Geschäft mit Elektronenröhren zu sprechen und Freunden der Röhrentechnik dadurch selten zugängliche, authentische Einblicke zu gewähren.
Im Rahmen von Gesprächen mit Stefan Müller, geführt um den Jahreswechsel 2022/2023, wurden Erinnerungen aus über 54 Jahren beruflicher Tätigkeit in der Welt der Röhren wieder lebendig und für die Nachwelt festgehalten.
Dieses Interview wurde auch in der GFGF-Vereinszeitschrift "Funkgeschichte", Ausgabe 271 und 272 veröffentlicht.
Die Fragen von Stefan Müller sind mit „M:“ gekennzeichnet, die Antworten von Heinz Ebert mit „E:“.
Tubelectron
M.: Im Jahr 1993 wurde die Firma Tubelectron in Ulm gegründet, um Röhren zu vertreiben. Wie kam es dazu?
E.: Im Jahr 1993 hat die AEG befunden, dass sich das Handelsgeschäft mit Röhren nicht mehr lohnt und wollte aus dem Geschäft aussteigen. Ich war bereits seit 1957 bei AEG-Telefunken tätig, davon viele Jahre als Vertriebsleiter für Röhren. So wurde ich damals, gefragt, ob ich daran interessiert sei, das Röhrengeschäft in Eigenregie weiterzuführen. Da mir das Geschäft mit den Röhren immer schon Freude gemacht hat, habe ich kurzerhand zugesagt und mit Freunden und Kegelbrüdern das nötige Geld dafür aufgetrieben. Zusammen mit meiner Frau Elisabeth habe ich dann noch im selben Jahr die Firma Tubelectron gegründet.
Ich habe dann den gesamten damaligen Bestand and Empfängerröhren, Senderöhren und Spezialröhren von der AEG übernommen, nicht jedoch Laufzeitröhren, Oszillografenröhren und andere Bildröhren. An Senderöhren waren zwar noch alte Bestände vorhanden, aber vergleichsweise wenig, weil das Sendröhrengeschäft bereits 1982 beim Vergleich an Siemens abgegeben worden war. Der Firmenname Tubelectron geht übrigens auf die Idee eines ehemaligen Kollegen aus der Exportabteilung, Dieter von Klinggräff, zurück, der leider schon lange verstorben ist. Er hat einfach das englische Wort „electron tube“ umgedreht zusammengesetzt. Zu Beginn lief Tubelectron noch auf den Namen meiner Frau Elisabeth, weil ich zunächst noch weiter bei AEG angestellt war und nicht gleichzeitig Geschäftsführer einer eigenen Firma sein konnte. Erst nach dem Dez. 1997, nach meinem Ausscheiden bei der AEG im Alter von 60 Jahren, lief Tubelectron auf meinen Namen.
Zu diesem Zeitpunkt konnte ich auf 40 Jahre Erfahrung im Vertrieb bei AEG-Telefunken zurückgreifen und war so gesehen bestens gerüstet. Und wie bereits erwähnt, hat mir das Geschäft mit Röhren einfach Freude bereitet. Ich habe das wirklich gern gemacht und es waren dadurch auch viele gute, persönliche Kontakte zu Kunden und Geschäftspartnern entstanden, die ich gerne fortführen wollte. Deshalb ist es dann auch nicht nur bei der Übernahme des Bestandes von AEG-Telefunken geblieben.
Ich habe z. B. Bestände von der Post, sprich dem Fernmeldetechnischen Zentralamt übernommen, die mir angeboten wurden, als die Post Ihren Anlagen auf Halbleitertechnik umgerüstet hatte. Darin waren z. B. große Mengen an Weitverkehrsröhren, z. B. C3m und C3g enthalten, welche die Post zuvor gekauft und als Ersatzteile eingelagert hatte. Auch eine größere Menge an EL156 waren dabei, die ja ausschließlich von Telefunken gebaut wurde. Die Mengen waren so umfangreich, dass ich einen Teil dieser Bestände sofort weiterverkaufen musste, um nicht in finanzielle Schieflage zu geraten. Einer der größten Abnehmer war damals Gert Müller von RSD in Frankfurt. RSD war damals nicht nur Handelsunternehmen für Röhren, sondern auch Generalimporteuer für Röhren aus der DDR. Wir kannten uns gut, denn bedingt durch die komplizierte Bürokratie kam es immer wieder zu Verzögerungen bei den Lieferungen aus der DDR. Dabei haben wir uns dann auch gegenseitig ausgeholfen. Das war eine interessante Zeit.
Natürlich war bei den übernommenen Beständen auch immer ein Anteil an Ladenhütern dabei. So waren z. B. im übernommenen Bestand von Heinze & Bolek große Mengen an deutschen und amerikanischen Militärröhren aus dem 2. Weltkrieg enthalten, sog. STEG-Ware, die kaum in nennenswerten Stückzahlen verkäuflich waren. (Anm: STEG steht für „Staatliche Erfassungsgesellschaft für öffentliches Gut“. STEG-Ware und bezeichnet militärische Produkte aus der Zeit des 2. Weltkrieges, die nach Kriegsende durch die STEG in Westdeutschland auf den freien Markt gebracht wurden, darunter auch viele Röhren aus ehemaligen Wehrmachtbeständen.)
Franz Heinze hat übrigens nach dem Verkauf seiner Bestände an mich das Geschäft nicht wie zuvor verabredet eingestellt, sondern wieder Ware aufgetrieben und bis wenige Jahre vor seinem Tod weiter mit Röhren gehandelt. Er ist 2020 im Alter von 98 Jahren verstorben.
M.: Im Jahr 1999 erschien die erste vollständige Preisliste von Tubelectron mit fast 3000 Röhrentypen, die erstmals auch an einen breiten Kreis von Kunden außerhalb der Industrie verschickt wurde, nämlich den bisherigen Kundenstamm der Fima Heinze & Bolek. Wer waren die bisherigen Kunden und welche neuen Kunden kamen nun hinzu?
E.: Die Sortierung und Erfassung der Lagerbestände und die Erstellung dieser Preisliste war ein Kraftakt, bei dem mich meine Familie und ehemalige Kollegen unterstützt haben. Das hat rund 1 Jahr gedauert. Danach hatte ich im Riedweg hier in Ulm gut 300 Regalmeter Röhren und das Palettenlager weitgehend verkaufsbereit.
In der Preisliste von 1999 waren neben den zwischenzeitlich erworbenen weiteren Röhrenbeständen von Behören, von Siemens und von ITT-SEL auch die 2 LKW-Ladungen an Röhren die ich von Heinze & Bolek gekauft hatte mit inbegriffen. Ich hatte mir bis dahin einen Kundenstamm aufgebaut, der im Wesentlichen aus kommerziellen bzw. gewerblichen Kunden bestand. Viele davon wurden von der AEG an mich verwiesen. Die AEG hatte außerdem ihre früheren Kunden darüber informiert, dass Tubelectron deren Röhrengeschäft übernommen hat und weiterführt. Darüber hinaus konnte ich auch mehrere bedeutende Großhändler als Kunden gewinnen. Dazu kam nun noch der Kundenstamm von Heinze & Bolek, der hauptsächlich aus Reparaturwerkstätten, Bastlern sowie „Jägern und Sammlern“ bestand, die wesentlich kleinere Mengen pro Type bestellten als meine bisherigen Kunden.
Insgesamt haben sich die Umsätze zunächst gut entwickelt. Ich habe die komplette Buchhaltung zusammen mit meiner Frau selbst gemacht und hatte so immer einen guten Überblick.
M.: Welche Marktaussichten für den Handel mit Röhren herrschten in den 1990er Jahren und wie ging es in den 2000er Jahren weiter?
E.: In den 90er Jahren war durchaus so viel Nachfrage, dass ich in Vollzeit beschäftigt war und ich zeitweise auch noch Hilfskräfte beschäftigen konnte. Das hat sich auch in den 2000er Jahren so fortgesetzt. Immerhin war ich zeitweise, zumindest für größere gewerbliche Kunden und Behörden, quasi Monopolist. So habe ich neben der deutschen Bundeswehr auch andere Streitkräfte im Ausland beliefert, z. B. in Schweden und Norwegen. Solche Anfragen habe ich immer gern wahrgenommen, zumal ich in der Lage war, die von den behördlichen Kunden geforderten Güteprüfungen spezifikationsgerecht durchzuführen. Hilfreich waren dabei frühere Kollegen, die als ehemalige Prüffeldleiter dankenswerterweise ihr Wissen bei mir einsetzt haben. Aber auch die Belieferung von Endkunden und die dadurch entstandenen Kontakte hätte ich nicht missen wollen.
Nach der Wende kamen dann nach und nach große Lagerbestände des Ostblockmilitärs auf den Markt, insbesondere aus der DDR. Da diese Ware aber hierzulande nur schwer verkäuflich war, habe ich mich beim Ankauf zurückgehalten.
In den 2000er Jahren konnte ich mit Tubelectron durchaus noch Jahresumsätze im unteren sechsstelligen Bereich erzielen.
M.: Gab es auch Sonderwünsche von kleineren Kunden?
E.: Jede Menge. Immer wieder wurde das Selektieren von Röhren angefragt, gelegentlich auch das Stempeln von Kundenmarken auf die Röhren. Es gab aber auch ausgefallene Anfragen wie z. B. das Nachvergolden von Kontaktstiften von einem Kunden aus dem Ruhrgebiet.
Die Spezialverstärkerröhren von Telefunken mit Pico 7 oder Pico 9 Sockel hatten ja früher meist vergoldete Stifte. Die hatten wir aber schon vor dem Zusammenbau der Röhre vergolden lassen. Das nachträgliche Vergolden war Neuland und nicht ganz einfach.
M.: Hatte Tubelectron nur NOS-Röhren im Programm oder auch Röhren aus neuer Produktion? Wenn ja, welche Typen, woher kamen die neuen und wie war die Qualität der neuen Lieferanten?
E.: Ich habe mich nach dem weitgehenden Wegfall der Lieferanten aus dem ehemaligen Ostblock umgeschaut, wo man die gefragten Typen noch herbekommen kann, und bezog dann in Kooperation mit anderen Röhrenhändlern Lieferungen aus chinesischer und in geringerem Umfang auch aus russischer Produktion. Das waren z. B. 6L6GC, 5881, 6550, EL34, KT88, 2A3, 211 und 845.
Elektronska Industrija in Jugoslawien hat zwar nach 1990 noch weiter produziert, durch das UN-Embargo von 1992 bis 2000 kam es aber immer wieder zu Lieferschwierigkeiten.
Als Ei dann irgendwann im Laufe der 2000er Jahre die Lieferungen ganz einstellte, kamen auch Vorverstärkertypen nur noch aus China und Russland. Es gab und gibt zwar noch JJ in der Slowakei, von dort haben wir aber kaum gekauft. Vorverstärkertypen musste ich auch nur in geringerem Umfang zukaufen, weil davon noch reichlich Altbestände verfügbar waren. Problematisch wurden nach dem Ende von Ei aber Typen wie die ECL86 und einige andere, die nie in China oder Russland hergestellt wurden.
M.: Wie kam es dazu, dass von Tubelectron auch noch Röhren mit den AEG-Logo verkauft wurden, verpackt in Schachteln, die ganz ähnlich aussehen wie die von Telefunken, auf denen aber ebenfalls AEG steht? Wurden Rechte an der Marke übernommen? Ab wann kamen diese AEG-Röhren auf den Markt?
E.: Die Röhren mit den AEG-Logo wurden nicht nur durch Tubelectron vertreiben, sondern auch vorher schon durch AEG-Telefunken selbst. Aber der Reihe nach:
Nachdem Telefunken 1982 in die Insolvenz ging und ein Vergleich geschlossen wurde, durfte die Marke „Telefunken“ aus rechtlichen Gründen nur noch für die Braune Ware verwendet werden, jedoch nicht mehr für Röhren. Wir haben deshalb von 1982 an „AEG“ auf die Röhren gestempelt, die wir verkauft haben. Auch die noch im Werk vorhandenen Verpackungen mit dem Telefunken-Logo konnten nicht mehr verwendet werden. Daraufhin habe ich die neuen AEG-Verpackungen unter dem Aspekt gestaltet, dass sie möglichst nahe an das alte Telefunken-Erscheinungsbild herankommen und sie in großen Stückzahlen bei der nahe gelegen Druckerei Höhn im Donautal fertigen lassen. Ich habe dann 1993 nicht nur Röhrenbestände von der AEG übernommen, die teilweise mit den AEG-Logo gestempelt waren, sondern auch die Stempelmaschinen und Stempelplatten mit allem Zubehör und auch alle nötigen die Mess- und Prüfgeräte samt Einschüben, hergestellt im werkseigenen Prüfmittelbau. Ich hatte drei Prüftische, von denen jeder in den 60er Jahren schon zwischen 30.000 und 40.000 DM in der Herstellung gekostet hat.
Auch die alten original Telefunken Stempelplatten hatte ich vor der Verschrottung bewahrt und mit übernommen.
M.: Zum Jahreswechsel 2011/12 hat Tubelectron schließlich den Geschäftsbetrieb eingestellt und die verblieben Bestände wurden an Jan Wüsten bzw. dessen Firma verkauft. Welches Resümee kann man aus den fast 2 Jahrzehnten Röhrenhandel in eigener Regie ziehen?
E.: Ich sage es noch einmal: Das Geschäft mit den Röhren hat mir immer große Freude bereitet und schon ein wenig wehmütig habe ich dann um Ostern 2012 aus gesundheitlichen Gründen meine nicht ganz kleinen Restbestände verkauft. Es waren immerhin noch 2 LKW-Ladungen mit ca. 300.000 Röhren und darüber hinaus noch die Mess- und Prüfgeräte sowie Stempelmaschinen und Stempelplatten.
Ich war sehr gut vernetzt und hatte aus der AEG-Zeit gute, über viele Jahre gewachsene Beziehungen zu Kunden und Lieferanten. Ich habe meinen Beruf auch schon bei AEG immer gern gemacht und ab 1993 habe ich schließlich den Beruf mehr und mehr zum Hobby gemacht und die Kunden nahtlos weiter bedient. Das war mir Antrieb über all die Jahre hinweg.
Arbeit bei AEG-Telefunken
M.: Wie eingangs erwähnt, waren 1997 schon Erfahrungen aus einem ganzen Berufsleben bei AEG-Telefunken gesammelt. Wie kam es Jahrzehnte zuvor zum Einstieg bei AEG-Telefunken und wie waren die Anfänge und Werdegang im damaligen Weltkonzern?
E.: Nach einer Lehre bei der Fa. Schwenk Zement habe ich im Januar 1957 als kaufmännischer Angestellter bei Telefunken in meinem Heimatort Ulm an der Donau im Vertrieb angefangen. Damals hieß die Firma noch Telefunken, ab der Fusion mit AEG im Jahr 1967 dann AEG-Telefunken und seit der Übernahme durch die Daimler AG 1985 nur noch AEG. Ich habe mich im Laufe der 40 Jahre Betriebszugehörigkeit hochgearbeitet. Zunächst zum Abteilungsleiter, dann zum Vertriebsleiter für Röhren in Deutschland und zuletzt weltweit. Als Vertriebsleiter hatte ich viele Entscheidungen zu treffen und schon damals habe ich die Entscheidungen so gewissenhaft getroffen, als ob es mein eigener Betrieb gewesen wäre.
M.: Ab wann war bei AEG-Telefunken das Ende der Röhrenära abzusehen und wie wurde darauf reagiert?
E.: Im Jahre 1973 ist in Deutschland der letzte mit Röhren bestückte Fernseher vom Band gelaufen und die Radios waren schon Jahre vorher auf Halbleiter umgestellt worden. Deshalb hat AEG-Telefunken 1973 die Produktion der Röhren für Radio und Fernsehen mit Ausnahme von Bildröhren eingestellt. Für das weiterlaufende Handelsgeschäft wurden dem entsprechend von nun an alle Röhren zugekauft, die wir nicht mehr in unseren Lagerbeständen verfügbar hatten. Der Abbau der Lagerbestände verlief von Type zu Type unterschiedlich schnell, so waren teilweise auch noch viele Jahre später Röhren aus original Telefunken Produktion im Vertrieb.
Die zugekauften Röhren wurden nach erfolgreich durchlaufenen Prüf- und Testmaßnahmen zunächst bei uns im Werk weiter mit Telefunken Logo gestempelt, und - wie bereits erwähnt - ab 1982 dann mit dem AEG-Logo.
Da die anderen Firmen in Westeuropa größtenteils schon vor uns die Produktion von Rundfunk- und Verstärkerröhren eingestellt hatten - zuerst ITT-SEL, dann Siemens und Philips-Valvo - mussten wir uns für das Handelsgeschäft weltweit, umschauen, wer noch die benötigen Typen herstellt. Wir wurden hautsächlich im Ostblock fündig.
Nachdem wir Lieferanten gefunden hatten, haben wir uns die entsprechenden Typen bemustern lassen. Wir haben die Muster dann untersucht und nach ihrer Qualität beurteilt.
Lieferanten war damals z. B. Elektronska Industrija „Ei“ in Niš / Jugoslawien, vor allem aber Tungsram in Budapest und RFT in der DDR, die bis zur Wende Röhren produziert haben. Rundfunk- und Verstärkerröhren hat RFT aus den Werken in Erfurt, Neuhaus und Mühlhausen geliefert, Senderöhren und Thyratrons aus Ostberlin. Ich war für die AEG mehrmals in der DDR bei der dortigen staatlichen Außenhandelsgesellschaft in Ostberlin, um Verträge über umfangreiche Röhrenlieferungen zu verhandeln und abzuschließen. Bezahlt wurde in DMVE (D-Mark Verrechnungseinheit), was zur Folge hatte, dass wenn wir viel von denen gekauft haben, die auch mehr bei uns gekauft haben. Bemerkenswert war dabei, dass die vorgelegten Verträge vorsahen, dass wir den Gegenwert von 5% des Liefervolumens als Provision an eine Vertragsverhandlungsgesellschaft in der Schweiz zu zahlen hatten. Wie ich später herausgefunden habe, gehörte diese Gesellschaft einem gewissen Alexander Schalck-Golodkowski.
Aber wir haben z. B. auch Muster von Röhrenherstellern in Indien besorgt, die sind aber bei der Prüfung durchgefallen. Die Qualität der Röhren aus Osteuropa hingegen, insbesondere der DDR war nicht schlecht, das muss man schon zugestehen. Die Werker waren gut ausgebildet und erfahren, aber es gab gelegentlich Schwierigkeiten bei der Beschaffung von Rohmaterialien. Das hat sich manchmal auf die Qualität ausgewirkt. Wir haben aber z. B. die EL34 mit vergleichbaren Qualitätszahlen wie wir sie früher selbst hergestellt hatten zu Hunderttausenden aus Mühlhausen bezogen und das zu einem Preis, für den wir selbst noch nicht einmal die Materialkosten hätten decken können.
Der Preis für diese Röhren war allerdings nicht nach betriebswirtschaftlichen Gesichtspunkten kalkuliert, sondern es war ein politischer Preis. Man war auf Devisen, auf Westwährung aus, die man zum Kauf von Westgütern benötigte.
Nach der Wende und dem Zusammenbruch des Ostblocks verschlechterte sich die Versorgungslage mit Röhren deutlich, weil viele der Werke dort die Produktion einstellten. Ich habe mich zwar damals zusammen mit Gert Müller von RSD in einem Brief an die Verantwortlichen bei der Treuhand gewandt, mit dem Ziel, die Röhrenfertigung in Mühlhausen zu erhalten, das war allerdings vergebens. Man hätte mit viel Geld einsteigen müssen, um das Werk am Laufen zu halten. Zu viel, als dass es sich je gelohnt hätte. Vor der Schließung haben wir nochmals 100.000 Stück EL34 liefern lassen.
Bei der Einstellung der Röhrenfertigung von Tungsram war ich in Budapest und habe auch dort große Bestände an Röhren gekauft. Tungsram hatte eine äußerst breite Typenpalette. Die haben nahezu alles produziert, egal ob sie die Lizenz dazu hatten oder nicht.
Diese Entwicklungen haben bei AEG dazu beigetragen, im Jahr 1993 aus dem Handelsgeschäft mit Röhren auszusteigen. So weit im Wesentlichen die Geschehnisse von 1973 bis 1993.
M.: Was war nach dem Ausstieg aus dem Handelsgeschäft mit Röhren der weitere Tätigkeitsbereich bei AEG.
E.: Zuletzt war ich dort für den weltweiten Vertrieb von Vakuumschaltkammern für Energieverteilungsanlagen verantwortlich. Die Technologie, die für den Bau dieser Schaltkammern nötig war, stammte weitgehend aus der Röhrentechnik und das Geld für die Entwicklung stammte größtenteils aus dem Handelsgeschäft mit den Röhren, das früher unter meiner Leitung lief.
Röhrenfertigung bei Telefunken und im Marktumfeld
M.: Telefunken unterhielt nach dem Krieg zwei deutsche Röhrenwerke, in Berlin und in Ulm. Gab es außerhalb Deutschlands noch weitere Werke?
E.: Nein, AEG-Telefunken hatte keine Röhrenfertigung im Ausland. Wir hatten nur unsere beiden Röhrenwerke in Berlin und Ulm.
M.: Wer hatte nach dem 2. Weltkrieg sonst noch Röhrenwerke in Deutschland in denen Rundfunk- und Verstärkerröhren hergestellt wurden?
E.: Siemens hatte sein Röhrenwerk in München, SEL-Lorenz hat in Esslingen bei Stuttgart produziert und Philips-Valvo hatte zwei Röhrenwerke in Hamburg. In der DDR gab es Röhrenwerke in Erfurt, Mühlhausen, Neuhaus am Rennweg und ist Ostberlin. Darüber hinaus gab es noch kleinere Betriebe und Labore, die auch Röhren hergestellt haben, wie z. B. die Firma Hiller in Hamburg-Eidelstedt, aber das waren keine großen Stückzahlen und nicht in industriellem Maßstab wie bei uns.
M.: Die industrielle Fertigung von Röhren ist selbst für heutige Verhältnisse ein aufwendiges und technisch anspruchsvolles Unterfangen. Was waren die Herausforderungen, die es zu bewältigen galt?
E.: Röhrenfertigung war technisch sehr anspruchsvoll, das konnte nicht jeder. Vor allem wegen der Präzision der Bauteile im Mikrometerbereich, die notwendig war. Besonders das erste Gitter musste sehr genau gefertigt und positioniert werden. Trotzdem gelang es uns, recht niedrige Auschusszahlen zu erreichen. Aber es kam auch vor, dass ganze Chargen verworfen werden mussten.
Die Glasverarbeitung und die Katodenchemie waren auch kritisch und natürlich der Zusammenbau der Systeme, der viel Feingefühl, eine ruhige Hand und sehr gute Augen erforderte. Die Systemmontage wurde deshalb ausschließlich von jungen Frauen gemacht und erfolgte teilweise unter dem Mikroskop.
Fehlermöglichkeiten gab es beim Röhrenbau fast unendlich viele, da ist alles Mögliche passiert. Schlechte Schweißstellen - von denen es in Röhren viele gibt - waren ein Problem, vor allem, weil sie oft nicht leicht zu entdecken waren. Das gab dann Wackelkontakte, die z. T. nur bei bestimmten Temperaturen erkennbar waren oder durch Anklopfen. Wir hatten auch Reklamationen, bei denen der Einkäufer des Kunde meinte: „Ihre Röhren haben Karies! Beim Herausziehen der Röhre bleiben die Stifte in der Fassung stecken!“
Schuld daran waren aber nicht in jeden Fall Probleme in unserer Fertigung, sondern oft auch zu stramme oder falsch ausgerichtete Kontaktfedern in den Fassungen, die die Kunden in ihren Geräten verbauten. Deshalb haben wir den Geräteherstellern sogenannte Stahlstiftphantome zur Verfügung gestellt. Damit konnten sie Kontaktfedern aufweiten, ausrichten und die Ein- bzw. Auszugskräfte vor dem Einsetzen der Röhren kontrollieren.
Wir hatten einen für damalige Verhältnisse relativ hohen Automatisierungsgrad in der Fertigung, z. B. in der Stanzerei, in der Glasverarbeitung und beim Einschmelzen. Dabei waren viele der Anlagen als Karusselle gebaut. Die Einschmelzautomaten mit ihren vielen Gasflammen standen im zweiten Stock, unweit meines Büros. Auf dem Weg ins Büro kam ich immer dort vorbei. Schön warm war es dort, vor allem im Sommer.
Wir hatten einen hohe Fertigungstiefe und haben z. B. alle unsere Stanz- und Biegearbeiten selbst gemacht. Die Stanzerei war im Parterre. Dort standen unzählige Maschinen und die waren nicht zu überhören. Die rohen Bleche und Drähte wie auch die Gläser wurden nach unserer Spezifikation von Zulieferern produziert und angeliefert.
M.: Wie muss man sich die Belegschaft eines Röhrenwerks vorstellen? Wie viele Leute arbeiteten dort in Ulm?
E.: In Ulm waren in den 1960er Jahren ca. 2500 Mitarbeiter im Röhrenwerk beschäftigt.
Neben der Produktion gab es einen Konstruktions- & Entwicklungsbereich und einen Musterbau, in dem die Röhren entwickelt und die ersten Muster hergestellt und erprobt wurden. Dann gab es eine große chemische Abteilung mit vielen Spezialisten, die sich um Dinge wie die Katodenbeschichtung, Isolierung der Heizfäden, Getter Materialien, Füllgase, die chemische Vorbehandlung und die technische Sauberkeit der Bauteile gekümmert hat. In der Vorfertigung gab es viele Bäder mit den unterschiedlichsten Chemikalien drin, die ständig überwacht werden mussten.
In anderen Bereichen der Vorfertigung wie der Stanzerei oder der Gitterwickelei und auch in der Glasverarbeitung wurden jede Menge Maschineneinsteller und -bediener beschäftigt. Und dann waren da noch ganze Säle voller junger Frauen, die die Systemmontage gemacht haben.
Nachdem die Systeme eingeschmolzen waren, kamen die Röhren in die Evakuierung, dann wurden die Kathoden aktiviert. Zuletzt ging es ins Prüffeld und zur Verpackung. Überall wurden fleißige Hände benötigt.
M.: Welche Röhren, die bei Telefunken entwickelt bzw. gebaut wurden, sind Dir besonders in Erinnerung geblieben?
E.: Da war z. B. die Elektrometerröhre YG1000. Die wurde als Nachfolgerin der T116 mit Magnovalsockel spezielle für Zeiss gebaut, zu Verwendung in Mikroskopen.
Die EL3010, eine Breitbandendpentode, die hauptsächlich als Treiberröhre für Kurzwellensender zum Einsatz kam, war auch aus Ulm. Sie war eine er letzten Neuentwicklungen im Bereich der Rundfunk- und Verstärkerröhren. Die wurde später auch noch als EL3010E mit Halbleitern für den Ersatzteilbedarf nachgebaut.
Die EL156 war eines unserer besten Pferde im Stall. Die wurde fast ausschließlich in Ulm gebaut, nur anfänglich kamen Mustermengen aus Berlin.
Von Interesse ist sicher auch die ECC803S. Wenn ich mich recht erinnere, wurde die aufgrund einer Anfrage von Rhode & Schwarz in Spanngittertechnologie entwickelt und bei uns in Ulm aufgelegt. Später wurde sie dann aber auch an andere Kunden aus dem Messgeräte- und Präzisionsinstrumente-Sektor geliefert, sie war aber keinesfalls für Rundfunk oder Musikverstärker gedacht und wurde auch nicht an Kunden aus diesem Bereich verkauft. Sie kostete damals immerhin das 3- bis 4-fache einer normalen ECC83.
Ich könnte noch mehr aufzählen oder nachschlagen, denn über unsere Produktionsmengen haben wir Buch geführt. Der Kollege Willi Becker und weitere Mitarbeiter waren über viele Jahre dafür verantwortlich dies für unsere beiden Werke zu erledigen. Ob alles immer hundertprozentig richtig erfasst wurde, da bin ich nicht sicher, weil das ja von Hand gemacht wurde. Ich habe aber diesen Aufschrieb mit dem Titel „Fertigung der Werke“ damals mitgenommen und später meinem Kollegen Siegfried Neumann übergeben, der ihn eingescannt im Internet verfügbar gemacht hat.
Sonst wären diese Aufzeichnungen wohl – wie so vieles andere – unwiederbringlich vernichtet worden.
M.: Welches waren die letzten Neuentwicklungen von Rundfunk- und Verstärkerröhren in Ulm und wann war das?
E.: Das waren die bereits erwähnte EL3010, die Universal-Leistungsröhren YL1260 und YL1350, sowie die 1 kW Senderöhre YL1510 in Keramikausführung. Die wurden auch in unseren hauseigenen Kurzwellensendern verbaut.
Als die Röhrenproduktion eingestellt und die Maschinen verschrottet waren, wurden die EL3010 dann unerwartet knapp. So haben wir zuletzt noch eine Halbleitervariante der EL3010E als Ersatz entwickelt und in Berlin bauen lassen, um unsere Sender noch weiter betreiben zu können. Die Sockel dazu kamen aus unseren Restbeständen in Ulm.
Mit diesem Unterfangen wurde allerdings einiges an Geld in den Sand gesetzt, weil kurz nach der Fertigung der EL3010E in dem Land, in dem die Sender betrieben wurden, das politische System kippte und die Sender außer Betrieb gingen.
Später entwickelte Typen für Farbfernsehgeräte wie die PL509 für die Bildröhren mit 90° Ablenkung und die PL519 für 110° Ablenkung wurden nicht mehr bei uns entwickelt, sondern fast nur noch bei Philips. Das Farbfernsehen war damals die Innovation schlechthin und ich war als Vertreter von Telefunken am 25. August 1967 vor Ort auf der Funk-Ausstellung in Berlin, als Willy Brandt medienwirksam den berühmten roten Knopf drückte.
Für die Produktion von Farbfernsehbildröhren hatte Telefunken in nur 15 Monaten auf der grünen Wiese ein komplett neues, hochmodernes Werk im Donautal in der Graf-Arco-Straße errichtet. Fertigungsanlauf war am 22.08.1967 und bereits 1972 waren 1 Million Bildröhren dort produziert worden.
Aber schon 1975 stagnierte die Nachfrage und Ende 1979, als 6,5 Millionen Farbbildröhren produziert waren, wurde das Werk an die Videocolor, eine Tochter der französischen Thomson-Brandt ausgegliedert und Anfang 1982 geschlossen.
Das war damals ein harter Schlag für die ehemaligen Kollegen und die Stadt Ulm. Und damit war auch die Fertigung von Röhren für die Braune Ware in Ulm vollends Geschichte.
Entwicklung und Herstellung von Rundfunk- und Verstärkerröhren
M.: Zumindest gängige Rundfunk- und Verstärkerröhren wie EL84 oder ECH81 wurden von allen etablierten Röhrenherstellern in Westeuropa hergestellt. Wie wurde erreicht, dass alle Hersteller die gleichen technischen Daten erreichten und die Röhren voll kompatibel waren? Gab es Qualitätsunterschiede?
E.: Das waren Gemeinschaftsentwicklungen, oft zwischen Philips, Siemens und Telefunken. Man hat bei Neukonstruktionen die Röhrendaten in technischen Gremien abgestimmt, um hinterher Röhren mit gleichen Werten produzieren zu können. Da wurden die Erstmuster auf den Tisch gelegt und verglichen und ggf. notwendige Änderungen besprochen. Was die Produktion anging, waren natürlich gewisse Anpassungen an den jeweiligen Maschinenpark notwendig, aber die elektrischen Werte der Röhren eines Typs waren genau gleich.
Vom Aufbau her gab die produktionsbedingten Unterschiede und die sieht man auch, wenn man die Röhren genauer anschaut oder zerlegt. Ein schönes Beispiel dafür ist die EL84. Wir haben unsere Anodenbleche rund, sprich zylindrisch gestanzt, die anderen haben sie eckig als Kastenanode ausgeführt.
Oder auch die EF86. Wir haben für die äußere Abschirmung ein normales Blech genommen, Philips-Valvo hat Lochblech verwendet.
Was die Qualität angeht, gab es kaum nennenswerte Unterschiede, zumindest wurden keine publik und auch bei unseren eigenen Untersuchungen haben wir nicht besonderes festgestellt. Es haben alle nur mit Wasser gekocht.
M.: Wie war die Vergabe der Bezeichnungen für die Röhren im Nachkriegseuropa geregelt, um zu verhindern, dass nicht plötzlich zwei Firmen für zwei völlig unterschiedliche Röhren ein und dieselbe Bezeichnung beanspruchen?
E.: Da gab es eine zentrale Stelle, die das europäischen Röhrenschlüssel verwaltete. Ab 1966 nannten die sich dann Pro Electron und waren in Brüssel angesiedelt. Dort musste die Bezeichnung für eine neue Röhre angefragt werden und von dort wurde die Bezeichnung dann vergeben. Das europäische Röhrenbezeichnungssystem mit den Gemeinschaftstypen der A-, B-, C-, D-, E-Reihe usw. wurde ja bereits 1934 auf Betreiben von Philips eingeführt. Aber schon Ende der 1930er Jahre kam es zu Problemen mit den verfügbaren Nummern in diesem Kodierungssystem und es wurde teilweise von 2 auf 3 Ziffern erweitert. Nach dem Krieg war es dann immer öfter so, dass vor allem bei den Pico-Röhren der E- und P-Serie die vorgesehen zwei Ziffern nicht ausreichten. Telefunken hat dann in den meisten Fällen neue, dreistellige Nummern mit einer Null zwischen der ersten und der dritten Ziffer beantragt, um einen größeren Nummernraum zu schaffen. Das galt bei uns sowohl für Rundfunktypen als auch für kommerzielle Typen. Auch bei der D-Serie haben wir das gemacht und bei kommerziellen Typen mit besonderen Eigenschaften wurde noch ein „S“ für „Spezial“ nachgestellt. Philips hingehen hat als neue Nummern für Rundfunktypen zunächst eher solche mit einer zusätzlichen „1“ als erste Ziffer beantragt.
So wurden z. B. die EF804 von uns und die EF183 oder die PCC189 von Philips entwickelt. Für die kommerziellen Typen hat Philips die Ziffern in die Mitte gezogen, wie bei E80F oder E88CC, bzw. mit drei Ziffern dann E288CC.
Später war das aber nicht mehr so eindeutig zuzuordnen, wer die Röhre federführend entwickelt hat, und bei Magnoval- oder Dekal-Typen hat man gleich von Beginn an drei Ziffern genommen, mit der Null an zweiter Stelle, vgl. PL500, EL503 usw.
Bestimmte Zahlenbereiche waren auch für die Neuentwicklungen der Röhrenwerke in der DDR reserviert. So z. B. dreistellige die mit „17“ begannen für die Gnomröhren wie EF174 und später die mit einer „6“ an zweiter Stelle für die kommerziellen Typen wie ECC960 oder EF861. Bei den kommerziellen D-Röhren gab es sogar zwei Bereiche. Zunächst wurde eine „1“ vorangestellt, wie bei DF191, dann wurde auch hier eine „6“ an zweiter Stelle verwendet, wie bei DF961.
Vertrieb von und Handel mit Rundfunk- und Verstärkerröhren
M.: Wie gestaltete sich der Vertrieb der Röhren aus Sicht der Hersteller.
E.: Es gab zum einen den Erstbestückungsbedarf bei den Geräteherstellern, die fast immer direkt bei uns gekauft haben. Da war von Akkord bis Zeiss alles dabei was Rang und Namen hatte. Zum anderen gab es die Großhändler, die die Bedarfe für das Ersatzteilgeschäft abgenommen haben. Die behördlichen Kunden haben auch oft direkt bei uns gekauft. Wir hatten Vertriebsniederlassungen, über die diese Geschäfte abgewickelt wurden. Dann gab es noch die innerbetrieblichen Abnehmer, also die Röhren, die bei AEG-Telefunken selbst in Geräte verbaut wurden.
M.: Wie waren die Beziehungen unter den Mitbewerbern? Es wird immer wieder behauptet, dass es Kooperationen oder so etwas wie ein Kartell zwischen den Röhrenherstellern gab.
E.: Zwischen den Röhrenherstellern gab es schon immer die eine oder andere Absprache, auch schon vor dem 2. Weltkrieg. Allein schon, um bei den Germeinschaftstypen auf die gleichen Daten zu kommen. Es muss Anfang der 1960er Jahre gewesen sein, als ein neues Kooperationsabkommen zwischen den großen Röhrenherstellern in Westeuropa geschlossen wurde. Neben AEG-Telefunken und Siemens in Deutschland, La Radiotechnique bzw. CIFTE in Frankreich und Mullard in Großbritannien waren noch weitere Röhrenhersteller in Westeuropa vertreten, allen voran aber Philips aus den Niederlanden. Die hatten durch ihre vielen Werke und regionale Marken wie Valvo, Miniwatt, Pope etc. den größten Anteil daran. Mullard gehörte auch zu Philips und CIFTE wurde ebenfalls von Philips übernommen. Philips hat mit seinen vielen Beteiligungen und Marken nicht immer mit offenen Karten gespielt: Die sind teilweise als Scheinkonkurrenten aufgetreten und haben uns mit ihrer großen Marktmacht immer wieder in Bedrängnis gebracht. Bei Telefunken gab es damals intern den Spruch: „Nimm Philips, oder gleich was Rechtes!“ Wir haben uns im Vertrieb eben immer ein wenig auf Kosten der Konkurrent amüsiert.
Wenn wir mit Philips im Gespräch waren, haben wir uns meistens in Hamburg einem Verwaltungsgebäude von Philips-Valvo in der Mönckebergstraße getroffen. Dort wurde z. B. abgesprochen, was man gegen die Firmen unternehmen kann, die bei Farbfernsehbildröhren die Systeme erneuert haben, was unserem Ersatzteilgeschäft abträglich war. Man hat dann beschlossen, dass beide Hersteller ihre Ersatzbildröhren zum halben Preis verkaufen, wenn die Kunden im Gegenzug die verbrauchte Bildröhre an die Hersteller zurückgeben. Diese Regelung wurde aber nach kurzer Zeit wieder aufgegeben.
Aber zurück zu dem Programm, bei dem es darum ging, die Fertigungsstückzahlen pro Röhrentype zu erhöhen und somit die Fertigungskosten zu drücken. Man hat also Stückzahlen zusammengelegt und im Rahmen eines Abkommens eine Art Ringtausch vereinbart. Jeder hat sich dadurch auf die Fertigung bestimmter Röhrentypen konzentriert und diese dann auch für die anderen Hersteller mitproduziert. Man hat dabei für jede Röhre einen bestimmten Wert festgelegt, auf dessen Basis man dann die Röhren untereinander getauscht hat. Wir von Telefunken haben am intensivsten mit Siemens kooperiert, aber auch mit den anderen. So haben wir bei Telefunken z. B. um 1967 aufgehört, die Typen EBF89, EF83, EL86, EM80 usw. zu produzieren und haben sie größtenteils von Philips-Valvo bezogen. Dafür hat Siemens z. B. die ECC82, ECC83, ECL82 und ECL86 von uns bezogen und bestimmte andere Typen an Philips-Valvo geliefert. Gelegentlich hat auch Tungsram Röhren aus unserer Produktion eingekauft.
So kam es dazu, dass Röhren oft nicht von der Firma hergestellt worden waren, deren Logo auf die Röhre gestempelt wurde.
M.: Wie wurden bei Telefunken die zugekauften Röhren im Vergleich zu denen aus der eigenen Produktion geprüft?
E.: Die Röhren, die wir von den Mitbewerberbern bezogen haben, liefen nicht über unsere Prüffelder, sondern deren Qualität wurde nur durch Stichproben überwacht. So wurde es später auch mit den Röhren gemacht, die wir nach Einstellung unserer eigenen Produktion für das Handelsgeschäft bezogen haben.
M.: Wie kann man erkennen, welche Röhren zugekauft wurden und welche nicht; oder ganz allgemein, wer welche Röhren hergestellt hat?
E.: Das in jedem Fall sicher zu erkennen ist das selbst für Insider nicht immer ganz einfach, aber es gibt einige Anhaltspunkte:
Wenn man einmal die meisten Hersteller in den USA, ein paar in Großbritannien, Lorenz und Telefunken ausnimmt, haben fast alle Röhrenwerke in der westlichen Welt, teilweise auch darüber hinaus, ein einheitliches Code-System verwendet, das heute Philips-Code oder Ätzcode genannt wird. Dieser Code wurde am Röhrenboden zwischen den Anschlüssen oder seitlich unmittelbar darüber angebracht und erlaubt unter anderem die Identifikation des Werkes, in dem die Röhre hergestellt wurde und den Herstellungszeitpunkt der Röhre.
Telefunken hat dabei aber meines Wissens nicht mitgemacht, obwohl für Telefunken ein entsprechendes Codezeichen zugeteilt bekommen hat. Bei Röhren aus unserer Produktion ist wohl die sogenannte „Raute“ im Pressteller, also dem Glasboden der Röhren, das bekannteste Merkmal, dazu aber später noch mehr.
Darüber hinaus gibt es noch weitere konstruktive Merkmale, wie die Ausführung der Kontaktstifte, des Systemaufbaus, des Glaskolbens, des Getters und des Sockels, sofern einer vorhanden war. Dabei ist allerdings zu beachten, dass mache der Einzelteile, aus denen die Röhren zusammengebaut wurden, auch ganz oder teilweise zugekauft wurden. Das macht die Sache nicht gerade einfach.
M.: Zusammenfassend kann man also sagen: Wenn auf einer Röhre ein bestimmtes Logo oder eine bestimmte Marke aufgedruckt ist, heißt das noch lange nicht, dass die Röhre auch von der entsprechenden Firma hergestellt wurde?
E.: So ist es. Und tendenziell kann man sagen: Je später die Röhre hergestellt wurde, umso wahrscheinlicher ist es, dass sie zugekauft wurde. Das gilt nahezu für alle Marken in der westlichen Welt inklusive USA.
M.: Was kann man aus der Sicht von Telefunken über die Qualität der zugekauften Röhren im Vergleich zu denen aus eigener Produktion sagen?
E.: Wie schon gesagt war bei den Zukaufröhren aus westeuropäischer Fertigung die Qualität durchaus vergleichbar. Aber auch die Ware aus dem Ostblock war nicht schlecht, soweit wir das festgestellt haben. Von einem Kollegen von Valvo habe ich einmal Ausschussgrenzen genannt bekommen, die etwas enger lagen als unsere, überprüfen konnte ich das aber nicht.
M.: In einem früheren Gespräch hatten wir schon einmal darüber gesprochen, dass es in Deutschland einen Mechanismus gab um die Marktanteile im Handelsgeschäft, also für den Ersatzteilmarkt für Röhren zu bestimmen. Wie funktionierte das?
E.: Jeder Hersteller hat seine Stückzahlen, die er im Handelsgeschäft abgesetzt hat an einen Notar in der Schweiz gemeldet. Der hat dann aufsummiert und die gemeldete Gesamtmenge allen Herstellern bekannt gegeben. So konnte sich jeder seinen Markanteil ausrechnen.
Das funktioniert aber nur, weil und solange alle mitgemacht haben.
M.: Wie waren die Markanteile für Rundfunk- und Verstärkerröhren in Deutschland Ende der 1950er Jahre und wie war deren weitere Entwicklung?
E.: Philips-Valvo hatte den größten Markanteil im Handelsgeschäft, dicht gefolgt von Siemens, dann kamen wir von Telefunken und den kleinsten Anteil hatte SEL (Standard Electric Lorenz).
Irgendwann kam dann auch Tungsram mit steigendem Marktanteil auf. Ab Mitte der 60er Jahren konnten dann die Handelsmarken und Importeure, wie RSD, Standard Brand, Industria, London, Hoges etc. verstärkt Fuß fassen.
M.: Warum gab es von SEL, einer Firma mit geringem Markanteil im Röhrengeschäft, ausfällig viele Alleingänge bei den Rundfunk- und Verstärkerröhren, wie die 70er Serie mit EEL71, EM71 usw. und spätere Röhren wie z.B. EM85, EMM803, ECLL800 usw., die aber relativ Breite Verwendung in Geräten fanden?
E.: Lorenz, die sich ab 1958 SEL, also Standard Electric Lorenz nannten und später ITT-SEL, hatten sich ihren Markanteil unter anderem auch dadurch erhalten, dass sie bestimmte Nischenmärkte besetzt haben und innovativ waren. Es gelang denen immer wieder gut, bestimmte Typen am Markt zu platzieren, für die sie Monopolist waren, um so „einen Fuß in die Tür“ zu bekommen. Hier kann man Anzeigeröhren als Beispiel nennen, wie die genannten Typen EM71, EM85 und EMM803, die es praktisch nur von SEL gab, aber relativ viel in Geräten verwendet wurden.
Die erste Pico 9 Doppel-Endpentode für Gegentaktbetrieb, die ELL80, war auch eine Entwicklung von Lorenz. Die wurde später zwar auch von anderen Firmen gebaut, aber dann hat Lorenz mit der ECLL800 bald noch ein Triodensystem für die Phasenumkehr mit im Kolben untergebracht und das hat dann kein anderer mehr gebaut außer Lorenz.
Außerdem war Lorenz ja ein Teil von ITT, einem amerikanischen Konzern, und so hatten die Zugang zu relativ günstig am US-Markt verfügbaren Typen, von denen sie auch gut hierzulande verkauft haben.
Die Amerikaner hatten anfangs stark auf die dort zuerst erschienenen Pico 7 Typen gesetzt und nur dann Pico 9 Röhren entwickelt, wenn die 7 Stifte nicht ausreichten. Eingeführt wurde Pico 9 mit den Doppeltrioden ECC82 und ECC83 bzw. 12AU7 und 12AX7, das waren die ersten Novaltypen in den USA und somit weltweit. Dafür reichten 7 Stifte nicht aus. So könnte sich erklären lassen, dass Lorenz bei den Pico 7 Typen die in den USA gängiger waren als bei uns, lange Zeit einen überdurchschnittlich hohen Marktanteil hatte.
Beispiel sind Röhren wie EF93, EF94, EK90 und EL90. Außerdem hatte Lorenz nach Kriegsende sehr schnell die 70er Loktal-Typen auf dem Markt, z. B. ECH71 und EEL71 und die entsprechenden U-Typen. Der Loktalsockel dieser Röhren stammt auch aus den USA.
Und noch etwas hat Lorenz anders gemacht als die anderen: Die haben ihre Röhren im Siebruckverfahren bedruckt statt sie - wie alle anderen - zu bestempeln. Das war von der Beschriftungsqualität her viel besser als das, was unsere Stempelmaschinen konnten.
Trotzdem waren Lorenz mit ihrem Röhrenwerk in Esslingen die ersten, die die Produktion von Rundfunk- und Verstärkerröhren in industriellem Maßstab in Deutschland eingestellt und dann nur noch zugekauft, sprich Handel getrieben haben.
M.: Wie war sonst das Verhältnis zu anderen Herstellern in Europa und weltweit?
E.: Es gab zwar zwischen der AEG und GE in den USA enge Beziehungen, die betrafen aber nicht das Röhrengeschäft. Da gab es keine Kooperation. Unser Röhrenwerk in Berlin hat allerdings zu Hochzeiten auch Rundfunk- und Verstärkerröhren in die USA geliefert, man wollte schließlich auch exportieren. Ein Beispiel dafür war die ECC83 und da gab es auch mal Schwierigkeiten. So hat uns das US-Kartellamt - wohl auf Betreiben der einheimischen Mitbewerber - nachgewiesen hat, dass wir ECC83 auf dem US-Markt zu einem niedrigeren Preis an die Kunden geliefert haben als in Deutschland. Dazu muss man sagen, dass das Preisniveau für Rundfunkröhren und den USA etwas niedriger lag als hierzulande. Trotzdem wurden wir wegen Verstoßes gegen ein Anti-Preisdumping-Gesetz verklagt und verurteilt, weil wir die ECC83 dort für 1,- $ auf den Markt gebracht hatten. Das waren damals ungefähr 4 DM. Diese Röhren hat man dazu mit doppelter Bezeichnung gestempelt, in diesem Fall stand dann z. B. ECC83/12AX7 auf den Röhren.
Wir haben auch einige US-Typen selbst gefertigt die keine europäische Bezeichnung hatten, z. B. 5U4GB, 6CB6, 6SN7, 6463 oder 7247. Letztere haben wir unter anderem an die Firma Fisher in den USA geliefert. Für mache US-Typen gab es auch hierzulande eine Nachfrage, wie z. B. durch die Bundeswehr, wo Geräte aus den USA verwendet wurden. Insgesamt war der US-Markt wegen des niedrigeren Preises zwar nicht besonders attraktiv, aber wir hatten auch ein Interesse daran, in Dollar bezahlt zu werden.
Philips hatte anfangs eine Kooperation mit Sylvania und RCA in den USA, hatte aber dann mit der Übernahme von Amperex dort auch eigene Werke. Am europäischen Markt war der Philips-Konzern - wie bereits erwähnt - mit zahlreichen Marken vertreten. Entweder unter der Hauptmarke Philips, wie z. B. in der Schweiz, in Italien und in den Niederlanden, wobei in den beiden letzteren teilweise auch die Marke Pope verwendet wurde. Oder unter Valvo in Deutschland, Mullard in Großbritannien, Adzam und Mazda in Belgien und so weiter. Der französische Markt war auch fest in der Hand von Philips mit Marken wie La Radiotechnique und zuletzt CIFTE.
Siemens hat ab Mitte der 1960er Jahre viele Röhren von uns und von Tungsram bezogen. Von Tungsram anfangs nur ältere, wie die Rimlock-Typen, später aber auch andere. Dann kamen immer mehr von Ei aus Jugoslawien. Im Laufe der Zeit war also immer weniger von Siemens, was mit Siemens gestempelt war. Von Siemens war uns auch bekannt, dass die im Handelsgeschäft die größten Rabatte gaben, um nicht an Markanteil zu verlieren. Siemens hat so z. B. über viele Jahre die Handelskette Interfunk, damals ein große Einkaufsgesellschaft des Einzelhandels, exklusiv mit Röhren beliefert.
Wir wurden - wie schon erwähnt - gerade bei den Farbfernsehtypen in den 1970er Jahren viel von Ei beliefert. Die hatten, wie in der DDR auch, ein zentralen staatlichen Vertriebskanal in Belgrad wo ich selbst auch zu Verhandlungen und Vertragsabschlüssen vor Ort war und mit Leuten aus dem Röhrenwerk in Niš zusammentraf.
Interessant bei den Lieferungen von Ei war damals, dass die Jugoslawen manchmal etwas unvorsichtig waren, was die Zusammenstellung der Sendungen anging. So haben wir einmal ein ganze Charge PL519 bekommen, mit Valvo gestempelt und in fertig in Valvo-Kartons verpackt. Philips hatte diese offenbar schon direkt dort stempeln und verpacken lassen. Beim nächsten Vertragsabschluss in Belgrad haben wir das dann auch so gemacht und den Jugoslawen Kartons und Stempelmaschinen zur Verfügung gestellt.
Ende der Röhrenära und Auswirkungen
M.: Was bedeutete der Untergang der deutschen Unterhaltungselektronikindustrie für den Geschäftsbereich Röhren bei Telefunken und allgemein? Gibt es einen direkten Zusammenhang mit der Einstellung der Röhrenproduktion in Deutschland, oder hatte das eher was mit dem Vormarsch des Transistors zu tun?
E.: Mehr das zweite als das erste. Das hing aber miteinander zusammen. Wie bereits erwähnt kam bei den Radios die Umstellung auf Halbleiter schon Mitte der 60er Jahre.
Ab diesem Zeitpunkt wurden auch die Röhren in den Fernsehgeräten immer weniger. Hatte man zunächst noch bis zu zwei Dutzend Röhren im Fernseher, wurden diese nach und nach durch Transistoren ersetzt, sobald die Transistoren für die notwendigen Frequenzen und Leistungen verfügbar waren. Durch die Farbfernseher kamen zwar wieder neue Röhren hinzu, das war aber nur von kurzer Dauer. Leistungsfähige Typen wie PD500 (später PD510), PL500 (später PL504), PL508, PL509 (später PL519), PY500A oder GY501 hielten sich bis Mitte der 70er Jahre in den Geräteneuerscheinungen. Empfängerröhren für Farbfernseher haben wir aber nur 7 Jahre lang produziert, von 1966 bis 1973. Nachdem dann, wie bereits erwähnt, 1974 in Deutschland so gute wie keine röhrenbestückten Geräte mehr neu auf den Markt gekommen sind, war unser heimischer Markt, auf den wir abzielten, bis auf das Handelsgeschäft quasi weggebrochen. Zeitgleich begannen deutsche Gerätehersteller Markanteile zu verlieren. So war es ganz logisch, die Produktion von Rundfunk- und Verstärkerröhren einzustellen, das wäre nicht mehr wirtschaftlich gewesen.
M.: Was passierte mit den Fertigungsanlagen der deutschen Röhrenwerke von Telefunken, als hierzulande die Röhrenproduktion eingestellt wurde? Es wird gelegentlich berichtet, dass diese in den Ostblock oder nach China gegangen sein sollen.
E.: Nachdem bei AEG-Telefunken die Produktion von Rundfunk- und Verstärkerröhren im Jahr 1973 endgültig eingestellt wurde, wurden unsere Fertigungsanlagen verschrottet. Von einem Verkauf von Anlagen ist mir nichts bekannt, das hätte ich wohl mitbekommen.
Man war bei der Verschrottung sogar so schnell, dass man in Berlin die Packmaschinen, mit denen Röhren in die Einzelschachteln verpackt worden waren und die Stempelmaschinen zuerst verschrottet hat. Dann wurden hunderttausende Röhren zu uns nach Ulm gebracht, um sie hier noch von Hand zu verpacken. Da fehlte es zum Schluss an der Abstimmung zwischen den beiden Werken.
M.: Gehen wir nun in die Zeit zurück, als noch Röhren produziert wurden, verschiedene Typen aber bereits ausgelaufen waren. Was passierte, wenn Kunden ausgelaufene Röhren nachfragten, die nur von Telefunken hergestellt worden waren und auch nicht mehr aus dem Lagerbestand geliefert werden konnten. Wurden Röhren nachträglich nochmal aufgelegt?
E.: Die EL156 zum Beispiel. Die Produktion wurde eigentlich 1971 eingestellt, doch bereits im Laufe des folgenden Jahres erhielten wir Anfragen von verschiedenen Kunden aus denen hervor ging, dass die 17.000 Stk. die wir 1971 noch produziert hatten nicht ausreichen würden. So haben wir dann Ende 1972 und bis zur endgültigen Fertigungseinstellung 1973 noch weitere 24.000 Stk. produziert.
Da gab es z. B. die Medizintechnikfirma DELMA aus Tuttlingen, die stellten Generatoren für Elektrokauter her. Das waren Skalpelle, in die Hochfrequenzströme geleitet wurden, um die entstehenden Wunden zu veröden. DELMA hatte nach unserer Abkündigung versucht, die 4 Stück EL156 in deren Hochfrequenzgeneratoren durch Halbleiter zu ersetzen. Das hat aber zunächst nicht so gut funktioniert, denn die Transistoren haben die starke Belastung, die bei einem Kurzschluss entstand, nicht lange genug überlebt und man wollte weiter die Röhren verwenden. So haben wir nochmal über 1000 Stk. EL156 dorthin verkauft. Ich erinnere mich noch gut, ich bin persönlich hingefahren und habe den Auftrag dafür vor Ort abgeschlossen.
Aber auch andere Röhren wurden nachträglich wieder aufgelegt.
Leider haben insbesondere Behören oft viel zu spät auf unsere Abkündigungen reagiert. Wir haben an das BWB, das Bundesamt für Wehrtechnik und Beschaffung in Koblenz die Abkündigungen geschickt und um die Mitteilung der Restbedarfe gebeten, um die Endfertigungsmenge festlegen zu können. Passiert ist aber erst einmal nichts. Die Nachbestellfristen, meist 6 Monate, ließ man verstreichen. Und dann kamen acht oder zehn Jahre später plötzlich noch unvereinbarte Nachbestellungen oder Ausschreibungen.
Da ist mir die YD1040 in Erinnerung, eine besonders impulsfeste Ausführung der 2C39BA. Die waren in transportablen Radargeräten der Bundeswehr verbaut, die für den Betrieb an provisorisch eingerichteten Flugplätzen gedacht waren. Die wurde von der Bundeswehr fünf Jahre nach Produktionsende in kleiner Stückzahl nachgefordert.
Und auch von der schon seit Jahren nicht mehr produzierten 6397spez. wurden 1972/73 nochmal 10.000 Stück hergestellt. Das BWB war ein Kunde, mit dem man es nicht leicht hatte. Mein damaliger Chef, Dr. Schenk, der im vergangenen Jahr leider verstorben ist, ist oft nach Koblenz gefahren, um vor Ort zu versuchen, Restbedarfe zu klären, hatte aber kaum Erfolg damit.
Mit der Post lief das wesentlich besser. Die wussten recht genau, was noch benötigt wurde und haben lieber etwas mehr Vorrat bestellt als zu wenig. Die übrig geblieben Restbestände kamen dann, wie eingangs schon gesagt, teilweise wieder zurück zu mir, sprich Tubelectron.
Die EbIII, eine kommerzielle Variante der AD1, wurde sogar mehrfach wieder aufgelegt. Sie wurde für Walzwerksteuerungen der AEG benötigt und daher auch nach dem Krieg von uns in Ulm immer wieder produziert, zuletzt sogar noch einmal 1972. Für den Außenkontaktsockel aus Pressstoff hatten wir zuletzt schon keine eigenen Werkzeuge mehr, den mussten wir zukaufen.
Handelsmarken und Ostimporte
M.: In der Nachkriegszeit tauchten verschiedene Handelsmarken im Röhrenmarkt auf. Welche gab es und wer steckte dahinter?
E.: Das gab es z. B. Ultron. Vor dem Krieg war das eine belgische Röhrenmarke, nach dem Krieg aber die Eigenmarke des Versandhändlers Bürklin. Der hat Ware von überall her bezogen und mit seiner Marke gestempelt. Da findet man Röhren aus der Produktion von Tungsram, Philips, Siemens und auch von uns, aber auch Ware aus Polen und DDR-Produktion sowie aus den USA und Großbritannien. Die haben es uns im Handelsgeschäft mit aggressiven Preisen nicht leicht gemacht. Bürklin gibt es heute immer noch und man kann dort auch heute noch Röhren kaufen, die Marke Ultron wird aber meines Wissens schon seit vielen Jahren nicht mehr zum Stempeln von Röhren verwendet. Wahrscheinlich hat man sich irgendwann die Kosten für das Umstempeln gespart.
Dann gab es meinen bereits erwähnten Freund Gert Müller, Röhrenhändler in Frankfurt am Main mit seiner Hauptmarke RSD und Nebenmarken wie FSG, PAN. Er war zuvor bei „Germar Weiss Großhandel / Import / Export“ beschäftigt, wo RSD als Abkürzung für „Röhren-Spezial-Dienst“ bereits als Marke genutzt wurde. Gert Müller hat sich 1975 dann mit RSD selbständig gemacht und hatte sehr gute Kontakte, vor allem in den Ostblock. Er war auch Generalimporteuer für Röhren aus der DDR. Gert war bis Mitte der 2000er Jahre im Geschäft, zuletzt hatte er seinen Betrieb nach Hofheim im Taunus verlegt und zum Schluss noch nach Ober Kostenz im Hunsrück. Er ist mittlerweile leider verstorben und seine umfangreichen Lagerbestände müssten an BTB in Nürnberg bzw. heute Fürth gegangen sein. BTB nutzt die Marke RSD noch heute.
Wenn wir gerade in Nürnberg sind, dort gab es mit Eugen Queck einen weiteren Händler und Ostimporteur mit Handelsmarken. Queck verkaufte unter eigenem Namen, später aber hauptsächlich über eine Kooperation mit Waldemar Witt unter der Marke EGRO. Mit Waldemar Witt habe ich mich gut verstanden. Auf seine Einladung hin war ich auch bei ihm zu Hause. Er war ein ausgesprochen netter Mensch und angenehmer Geschäftspartner, der leider viel zu früh verstarb. Außerdem wurde von Queck die Marke Standard Brand genutzt, einerseits um amerikanische Typen bei uns zu vertreiben, aber auch um den US-Markt zu bedienen. Diese Röhren wurden meist aus den USA importiert, aber nicht nur. Queck und Witt haben bei uns, also bei AEG-Telefunken, auch Röhren gekauft, hauptsächlich gestempelte, und haben die unter unserer Marke weiter vertrieben. Aus dem Unternehmen von Eugen Queck entstand 1981 die Firma BTB mit Herbert Ballwieser und Christa Thomanek an der Spitze. Mit beiden hatte ich über Jahrzehnte hinweg geschätzte Geschäftspartner, denn sie waren schon unter Queck tätig.
Neben den bereits genannten gab es noch zahlreiche weitere Handelsmarken, wie HOGES, Inter, Union, Industria, METAL, STAAR, Radio RIM, Heninger Service und viele mehr. Darüber hinaus gab es auch welche, die aus Großbritannien kamen wie LONDON, Haltron oder Zaerix. Die Röhren dieser britischen Marken mussten aber nicht unbedingt dort hergestellt worden sein. Auch die haben offensichtlich Ware aus dem Ostblock bezogen.
Die Röhren der Marke Industria kamen, wie man anhand des Namens leicht erraten kann, von Elektronska Industrija in Jugoslawien. Wo HOGES, INTER und UNION her kamen weiß ich nicht mehr, ich hatte aber unter Tubelectron Restbestände dieser Marken verkauft und die Rückmeldung der Kunden bzgl. der Qualität war eher durchwachsen.
Als Sonderfall kann man noch TEKADE in Nürnberg zu erwähnen. Die haben in der unmittelbaren Nachkriegszeit viele Ersatzröhren, also Umbauten auf der Basis von Wehrmachtröhren gefertigt und möglichweise auch noch in geringen Umfang bis Mitte der 1950er Jahre selbst Röhren hergestellt, danach war TEKADE für Röhren aber nur noch eine Handelsmarke unter der hauptsächlich aus dem Philips-Konzern zugekaufte Röhren vertrieben wurden.
Telefunkenröhren aus heutiger Sicht: Qualität und Besonderheiten
M.: Telefunkenröhren genießen bis heute, vielleicht sogar heute mehr denn je - einen ausgezeichneten und herausragenden Ruf, insbesondere in audiophilen Kreisen. Oft hört man die Aussage, dass der Klang der Telefunkenröhren der beste sei und bis heute unerreicht. Wie könnte man sich das erklären?
E.: Das kann ich nicht wirklich erklären! [lacht]
Ich selbst hatte schon den Eindruck, dass die Röhren von Valvo zumindest teilweise qualitativ eine Spur besser waren als die von uns. Die hatten womöglich auch ein wenig engere Ausschussgrenzen als wir.
Aber der Name Telefunken war schon etwas Besonderes. Er stand jahrzehntelang für ein deutsches Vorzeigeunternehmen, das technologisch führend war und viel erreicht hat.
M.: Was ist das Besondere an Röhren von Telefunken (Eigenproduktion)?
Was hat Telefunken technisch anders gemacht als die Mitbewerber?
E.: Das ist immer ein Geheimnis geblieben, auf allen Seiten. Die technischen Daten waren zwar wie bereits besprochen genau gleich, wir wussten aber nicht im Detail, ob und wie die Konkurrenz bei den nicht sichtbaren technischen Feinheiten etwas anderes gemacht hat als wir.
M.: Zu Beginn hatte Telefunken für die nach dem Krieg neuen, ungesockelten Röhren eigene Bezeichnungen. Miniaturröhren wurden Pico 7 genannt, Rimlock-Röhren Pico 8 und Novalröhren Pico 9. Was hat es mit der sog. Raute (die eigentlich ein Quadrat ist) auf sich, die man an im Glasboden dieser Röhren erkennen kann?
E.: Das angedeutete Telefunken Markenzeichen im Pressteller der Röhren war als eindeutiges Wiedererkennungszeichen für uns gedacht. Die Stempelung war ja nicht besonders dauerhaft. Es wurde im Laufe der beiden Jahre 1955/1956 nach und nach in unserer Produktion eingeführt. Das Zeichen ist übrigens auch bei den Magnoval-Typen aus unserer Produktion zu finden.
M.: Hat Telefunken die gleiche Röhrentype selbst auch ohne Raute im Glasboden produziert oder gab es Zukauf von Presstellern?
E.: Telefunken hat seine Pressteller selbst hergestellt und die wurden zumindest ab Ende 1956 durchgehend mit dem angedeuteten Markenzeichen versehen. Ich möchte aber nicht ausschließen, dass es in Ausnahmefällen kurzzeitig auch Zukauf von Presstellern gab oder man kurzzeitig Werkzeuge bei der Presstellerherstellung einsetzen musste, die das angedeutete Markenzeichen nicht drin hatten. Wir haben aber keine unserer selbst hergestellten Pressteller an andere Röhrenhersteller geliefert.
M.: Manchmal sind Ziffern in der Raute zu sehen. Was hat es damit auf sich?
E.: Nicht viel, das sind nur Werkzeugnummern. Die machten nachvollziehbar, in welchem Werkzeugeinsatz ein Pressteller hergestellt wurde. Wenn ein Produktionsfehler an einem Pressteller erkannt wurde, der auf Beschädigung oder Verschleiß am Werkzeugeinsatz zurückzuführen war, konnte man den damit leicht zuordnen und den schlechten Einsatz schnell erneuern.
M.: Wurde diese Raute intern bei Telefunken auch „Raute“ genannt?
E.: Nein, das Telefunken Markenzeichen wurde intern nicht so genannt. Das alte Markenzeichen von Anfang der 30er Jahre, das noch 8 Ecken hatte, wurde manchmal Telefunken-Stern genannt, aber ich denke, dass die Bezeichnung „Raute“ nicht von Telefunken selbst stammt. Das hat wohl jemand außerhalb der Firma erfunden.
M.: Warum wurden die Röhreneinzelverpackungen bei Telefunken eine Zeit lang zusätzlich in Zellophanfolie eingeschweißt?
E.: Das wurde gemacht, um dem Einzelhandel folgende Betrugsmasche zu erschweren:
Manch findiger Einzelhändler oder Werkstattbetreiber hat seinen Kunden, den Gerätebesitzern, gebrauchte Röhren in neu aussehenden Kartons als Neuware verkauft. Das führte dann zum baldigen Ausfall, die Kunden kamen und beschwerten sich. Schuld für die schlechte Röhre hatte natürlich der böse Hersteller. Daraufhin reklamierte der Einzelhändler über den Großhandel bei uns oder der Kunde wurde zur Reklamation bei uns ermuntert, weil man ja noch innerhalb der damals 6-monatigen Gewährleistungsfrist war. Das schädigte nicht nur unseren Ruf, sondern verursachte uns auch nicht unerhebliche Kosten. Nicht nur für die Ersatzröhren, die wir liefern mussten, sondern auch für die Reklamationsbearbeitung. Das wollten wir abstellen. Der Kunde sollte durch die unbeschädigte Folie sehen können, ob die Röhre wirklich fabrikneu war.
Leider haben die anderen Röhrenhersteller dabei nicht mitgemacht. Der Einzelhandel mied uns daher und wir verloren Marktanteile im Handelsgeschäft. Deshalb haben wir die Folie nach einiger Zeit wieder abgeschafft.
Denselben Zweck wie diese Folie hatten zuvor auch die Hohlnieten, die Anfang der 1950er Jahren von uns, und die Heftklammern die etwa im selben Zeitraum von Valvo angewandt, jedoch nach ein paar Jahren auch wieder aufgegeben wurden. Damit wurden die Röhrenschachteln verschlossen, um erkennbar zu machen, ob sie vorher schon geöffnet worden war. Diese Idee wurde Jahre später von manchen Handelsmarken wieder aufgegriffen, z. B. von Hoges.
Eine andere Masche war, dass die Röhren in den Geräten kurz vor Ablauf der Gewährleistung gegen neue ausgetauscht wurden und die gebrauchten als zu schwach reklamiert wurden. Normalerweise haben wir die reklamierten Röhren nicht elektrisch geprüft und direkt durch neue ersetzt. Nachdem aber die Reklamationen über Großhandel immer mehr zunahmen, habe ich irgendwann eine Aktion gestartet:
Unter den Rückläufern wurden bestimmte Röhrentypen definiert, von denen wir für eine bestimmte Zeit alle in unser Prüffeld gegeben haben. Dabei stellte sich heraus, dass 60% der Rückläufer einwandfrei und gar nicht reklamationswürdig waren. Wir sind dem begegnet, in dem wir die Verträge mit den Großhändlern geändert haben: Wir haben Garantieablösung, kurz Gabl., vereinbart und als Kompensation 3% im Preis nachgelassen, so wie es auch größtenteils schon bei behördlichen Kunden üblich war. Damit war gegenüber uns keine Einzelreklamation mehr möglich. Telefunken war Vorreiter bei der Garantieablösung gegenüber dem Großhandel. Es hat uns Markanteile gekostet aber auch viel Kosten erspart.
Bei den Behörden betrug der Gabl.-Nachlass 2,5%. Zeitweise wurden die Röhren, von denen ganze Chargen an die Behörden geliefert wurden, auch mit dem Schriftzug „Gabl“ gestempelt, um dies kenntlich zu machen. Bei kleineren Mengen war dies wegen des Mehraufwandes für das Stempeln nicht üblich.
M.: Wie bereits angesprochen haben Philips und viele andere Hersteller Ihre Röhren mit einem Code gekennzeichnet. Telefunken hat ein eigenes Codesystem gehabt. Warum ein eigener Code und warum war der so kompliziert?
E.: Da muss man unterscheiden: Der Code von Philips war ein Herstellungscode, unser Code war ein Stempelcode.
Philips und die vielen anderen Hersteller, die den Code von Philips verwendet haben, haben damit neben der Röhrentype und deren Revisionsstand, das Produktionswerk und den Herstellungszeitpunkt codiert. Wie bereits erwähnt hat Philips uns zwar für ihr Codesystem auch einen Werkscode zugeteilt und wir hätten somit den Philipscode auch verwenden können, haben das aber soweit ich weiß, nie getan.
Wir haben im Gegensatz dazu neben dem Revisionsstand der Röhre Ort und Zeitpunkt der Stempelung codiert. Man muss wissen: Die Röhren können bei uns durchaus Monate, manchmal auch Jahre im Lager gelegen haben, bevor sie gestempelt wurden und bis zur Auslieferung kann weitere Zeit vergangen sein, besonders bei Typen, die in geringeren Stückzahlen liefen. Die liefen nicht in jeder Woche vom Band.
Warum der Telefunken Stempelcode so ist, wie er ist, kann ich nicht sagen, das wurde vor meiner Zeit definiert, es gab aber im Grunde vier verschiedene Stempelcodesysteme bei Telefunken. Das erste wurde bis Kriegsende verwendet und bestand nur aus 2 Kleinbuchstaben, in denen der Herstellungsmonat und das Herstellungsjahr codiert waren. Das zweite Codesystem wurde von 1945 bis 1958 verwendet und stellte eine Erweiterung des ersten dar. Vor die beiden Kleinbuchstaben kam ein Großbuchstabe für das Werk. U für Ulm oder B für Berlin. Und 2 Ziffern wurden hintenangestellt, um die Revision der Röhren anzugeben.
Ab 1958 wurde ein neues, drittes Codesystem eingeführt. Es begann wieder mit U oder B, dann folgten bis zu 7 Ziffern und wenn es sich um eine Vorserienfertig handelte, wurde noch ein Großbuchstabe nachgestellt. Mit den Ziffern wurde das taggenaue Datum der Stempelung und die Revision der Röhre angegeben. Wie der Übergang vom alten auf das neue System im Einzelnen vonstattenging, kann ich nicht mehr sicher sagen, er zog sich aber über einen Zeitraum von vielen Jahren hin. Im alten System waren noch Kleinbuchstabenkombinationen bis Dezember 1968 vorgesehen.
Schließlich wurde ab 1964 noch parallel noch ein viertes Codesystem allein für Zukaufröhren eingeführt, welches aus nur 5 Ziffern bestand und den Tag der Stempelung beinhaltete. Bis 1964 wurden für Zukaufröhren dieselben Codesysteme verwendet wie für die Eigenproduktion.
M.: Man findet auch original verpackte Telefunken Röhren, bei denen der Stempelcode zwar auf der Röhre, nicht aber auf der Schachtel zu finden ist. Was hat es damit auf sich?
E.: Viele Jahre lang hat man in der Nachkriegszeit den Stempelcode nicht nur auf die Röhren, sondern auch auf die Einzelverpackungen gedruckt, wobei das B bzw. das U für das Werk auf den keinen Schachteln des Platzes wegen weggelassen wurde.
Irgendwann Mitte der 1960er Jahre hat man aber nach und nach damit aufgehört, und zunächst neben der Typenbezeichnung nur noch eine Ziffer für die Herkunft auf die Schachteln gedruckt, später wurde auch die weggelassen.
In den Fällen, wo nur eine Ziffer außer der Typenbezeichnung auf der Schachtel vorhanden ist, ist deren Bedeutung wie folgt:
Die „1“ steht für Ulmer Eigenproduktion, die „2“ für Berliner Eigenproduktion mit Berlinhilfe und die „3“ für Berliner Eigenproduktion ohne Berlinhilfe. Ob bzw. für was die „4“ genutzt wurde weiß ich nicht mehr. Die „5“ Stand jedenfalls für Zukauf außerhalb des Ringtauschabkommens und die „6“ für Zukauf innerhalb des Ringtauschabkommens, oder „aus Integration“ wie wir das genannt haben. Das waren meist Röhren von Siemens, aber auch von Philips-Valvo. Weitere Ziffern wurden meines Wissens nicht verwendet.
Man kann somit anhand dieser Ziffern erkennen, woher die Röhre stammt, ohne die Schachtel öffnen zu müssen.
Die Berlinhilfe war übrigens eine Art Subvention, die Unternehmen bekommen haben, die in Westberlin produziert und nach Westdeutschland geliefert bzw. dort verkauft haben.
M.: Warum wurden einige Röhren ausschließlich von Telefunken gebaut und nicht auch von anderen? Und warum wurden diese Röhren dann unter anderen Marken verkauft, so z.B. die EL156, die auch unter der Marke Siemens verkauft wurde. Wie kam es dazu?
E.: Entweder wollten wir alleiniger Hersteller bleiben oder die anderen wollten nicht in eine Eigenproduktion investieren. Und dann gab es ja noch das Ringtauschabkommen. Darüber hat Siemens die EL156 bei uns ungestempelt gekauft und hat dann selbst gestempelt und verpackt.
Bei den Stahlröhren - und hier meine ich die, die wirklich ein Stahlkolben haben - sind wir bei vielen Typen Alleinlieferant geblieben. Philips hat zwar für kurze Zeit auch Stahlröhren hergestellt, aber nur wenige Typen. Darüber hinaus wurden kompatible Ausführungen mit Glaskolben hergestellt, z. B. von Tungsram und in der DDR, aber nicht für alle Typen.
Beispiele für weitere bekannte Nachkriegsröhren, bei denen wir alleiniger Hersteller waren, sind EC8020, ECF8070, ECL113, ED8000, EF410, EF804, EF804S, EF805S, EL13, EL5000, EM5, EM35, EMM801 und EZ150.
M.: Andererseits gibt es Röhren wie E810F, EL90, EZ81 oder EL503, die zwar unter der Marke Telefunken verkauft, aber nie von Telefunken gefertigt wurden. Auch aus der Vorkriegszeit gibt es Beispiele, wie die EB1. Warum?
E.: Das hat sich für uns schlicht nicht gelohnt und man hat das bereits erwähnte Ringtauschabkommen ausgeweitet. Die EL503 kam ja erst ganz spät, etwa 1966 auf den Markt, und die E810F nur wenig vorher. Da wollen wir nicht mehr selbst in neue Werkzeuge investieren. Auch Philips hat diese Röhren damals nicht mehr in mehreren Werken produziert. Soweit ich heute weiß, kamen alle EL503 aus einem einzigen Werk in Frankreich.
M.: Von den EL503 gibt es auch welche, auf denen die Telefunken Stempelung auch die Herkunftsangabe „Made in Germany“ umfasste. Nahm man es mit der Herkunftsangabe damals nicht so genau?
E.: Wenn wir mit Philips zu tun hatten, so lief das fast immer über Valvo in Hamburg. Von dort aus wurden auch die zugekauften Röhren an uns geliefert. Wir haben daher unterstellt, dass sie in Hamburg, sprich in Deutschland hergestellt wurden. Philips hat sich da nicht in die Karten schauen lassen. Vieles ist erst im Nachhinein als Tageslicht gekommen.
M.: Selbst viele Mitarbeiter der betroffenen Firmen waren über diese Praxis des Zukaufs und der Stempelung von Zukaufröhren offenbar in Unkenntnis. So gibt es einen Bericht, dass Ingenieure von Valvo vermeintlich ‘eigene‘ Röhren aus dem Handel zurückgekauft haben, um ein potenzielles Qualitätsproblem zu untersuchen, dabei aber zu ihrer Überraschung feststellten, dass die gekauften „Valvo-Röhren“ von Siemens hergestellt worden waren. Was kannst Du dazu sagen? Wie bekannt war das Ringtauschabkommen unter den Mitarbeitern von Telefunken, die jetzt nicht gerade im Vertrieb oder Einkauf gearbeitet haben?
E.: Wir haben das nicht breitgetreten. Solange wir noch selbst produziert haben, dürfte das nur den Kollegen bekannt gewesen sein, die direkt damit zu tun hatten, also im Vertrieb, im Einkauf, im Wareneingang und in der Chefetage.
M.: Aufgrund der mannigfaltigen Informationen möchte ich noch einmal zusammenfassend fragen, was bei der Unterscheidung zwischen Röhren aus Eigenproduktion von Telefunken und zugekauften Röhren zu beachten ist?
E.: Das angedeutete Telefunken Markenzeichen im Glasboden, das heute Raute oder Diamond genannt wird ist sicher ein verlässlicher Hinweis auf Eigenproduktion. Fehlt es, so handelt es sich mit großer Wahrscheinlichkeit um Zukauf oder um alte Produktion von vor 1957. Solch alte Produktion ist jedoch bereits zu Zeiten von Tubelectron so gut wie nicht mehr im Markt aufgetaucht. Mir ist allerdings zu Ohren gekommen, dass es Fälle gegeben hat, bei denen durch Dritte versucht wurde, das Zeichen nachträglich mit Hilfe eines Laserstrahls anzubringen, um vorzutäuschen, dass die Röhren von Telefunken gefertigt worden sei. Das lässt sich jedoch bei genauem Hinschauen ganz gut unterschieden, denn das originale Markenzeichen ist erhaben, was man mit dem Laser nicht hinbekommt. Der verursacht eher einen Materialabtrag.
Auch der von uns verwendete Stempelcode kann zur Unterscheidung genutzt werden. Besteht der nur aus 5 Ziffern, sind es Röhren aus Zukauf. Ist ein andersartiger Code vorhanden, wie zuvor bereits näher erläutert, deutet dies auf Eigenproduktion hin. Die Bedeutung des Codeaufdruck auf den Einzelverpackungen haben wir auch schon besprochen; die kann auch zur Unterscheidung beitragen, ohne dass die Schachtel geöffnet werden muss.
Trotzdem ist auch hier genaues Hinsehen gefragt, denn auch die Bedruckung von Schachteln und die Bestempelung von Röhren können nachgemacht werden. Schließlich kann man sich noch technische Details anschauen, wie den Systemaufbau, die Einschmelzstelle oder die Formgebung der Anodenbleche und der Glimmerscheiben. Und was man auf jeden Fall noch sagen: Wenn ein Philips-Code auf der Röhre ist, der meistens eingeätzt wurde, ist sie nicht aus unserer Eigenproduktion.
M.: Noch eine Frage zum Schluss:
Es wurde der Vorwurf erhoben, dass bei Tubelectron Röhren durch Umstempeln „gefälscht“ worden seien. Trifft das zu?
E.: Wie bereits erwähnt, haben wir tatsächlich größere Mengen an Röhren zugekauft und selbst gestempelt oder stempeln lassen. Das war bei AEG so und später auch unter Tubelectron.
Es wurden sowohl Röhren gestempelt, die ungestempelt von den Werken kamen, von denen wir sie gekauft hatten, als auch bestehende fremde Stempel entfernt und durch unsere ersetzt. Insofern kann man von Umstempeln sprechen, wobei das Entfernen der bestehenden Stempel extra Arbeit bedeutete und wir deshalb die Röhren, die wir stempeln wollten, möglichst ungestempelt bezogen haben. Wir haben darauf geachtet, dass die Qualität der Röhren stimmt und deshalb sehe ich das nicht als Fälscherei an, ganz im Gegenteil. Es war spätestens seit Mitte der 1960er Jahre in Westeuropa im Rahmen des Ringtauschabkommens gang und gäbe, Röhren anderer Hersteller mit der eigenen Marke zu stempeln. Wenn man also 1966 eine Röhre mit Telefunken-Stempel gekauft hat, war die Wahrscheinlichkeit nicht gering, eine Röhre aus Fremdproduktion zu bekommen. In den Jahren danach wurde die Wahrscheinlichkeit, Fremdproduktion zu bekommen immer größer. Nach dem Ende unserer Fertigung 1973 gab es zwar noch den Verkauf aus Lagerbeständen, aber sonst nur noch Fremdproduktion und das war - wie gesagt - nicht nur bei Telefunken so. Vergleichbares war vom europäischen und auch vom amerikanischen Markt bekannt.
Markenrechte
M.: Was passierte mit den Markenrechten von AEG und Telefunken in Bezug auf Röhren bis heute?
E.: Die Rechte für die Marke Telefunken liegen bei der TELEFUNKEN Licenses GmbH in Frankfurt, quasi dem Nachfolger unserer dort ansässigen Patentabteilung. Das gilt auch für Röhren und diese Rechte werden auch bei heute wahrgenommen. Mir ist ein Fall bekannt, bei dem ein US-Amerikaner EL34 aus DDR-Produktion mit „Telefunken“ gestempelt, in Wellpappe eingewickelt und mit einer Telefunken-Banderole versehen hat. Der wurde von den Frankfurtern mit Erfolg verklagt. Ich weiß davon, weil ich zu Tubelectron-Zeiten den Auftrag aus Frankfurt erhielt, ein Gutachten über die Herkunft dieser Röhren zu erstellen.
M.: Das waren nun viele Stunden voller interessanter Einblicke und voller reichhaltiger Informationen. Ich danke vielmals für die Zeit und die Bereitschaft zu diesem Gespräch.
E.: Gern geschehen. Es war auch für mich eine interessanter Ausflug in die Vergangenheit voller wiedererwachter Erinnerungen.
[Stefan Müller, Boxberg, im Januar 2024]
Für diesen Post bedanken, weil hilfreich und/oder fachlich fundiert.
Röhrenhandel in Deutschland - Erinnerungen eines Insiders
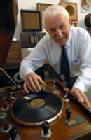
Hochinteressant und lesenswert! Dieses Interview ist auch in der GFGF-Zeitschrift "Funkgeschichte" Nr. 271 und 272 auf 18 Seiten zu lesen, dazu 32 aufschlussreiche Bilder.
Wolfgang Eckardt
Für diesen Post bedanken, weil hilfreich und/oder fachlich fundiert.